Более мощные ветряки
Пусть есть ветряк, который может что-то вращать. Вращать он должен такую штуковину:
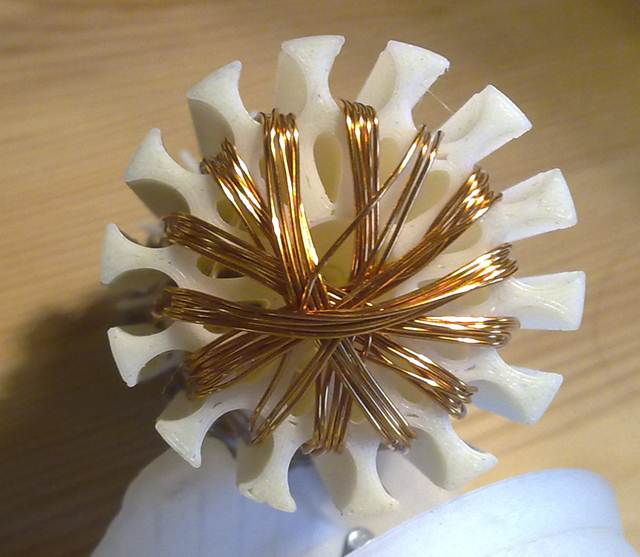
… расположенную между магнитами. От того, сколько провода намотано, зависят характеристика двигателя. Или генератора. Устройство одно и то же. Но если подключить ток, то будет вращение. А если вращать, то на контактах появится напряжение.
Здесь сразу видно, что если надо намотать очень много проводов, они могут просто не поместиться в круглые пазы. Чтобы получить нужный двигатель, придётся либо увеличивать «катушку» (это больший вес, особенно если она металлическая) либо уменьшать сечение проводов (из-за этого у них будет больше сопротивление и тоже большие потери энергии не на работу).
Я не знаю, когда появилась тонкая лаковая изоляция провода. Если позже чем обычная резиновая, то это - самое развитие технологий, которое позволило принципиально улучшить качество двигателей (больше провода можно засунуть в якорь или якорь можно сделать меньше, или провода толще, что снизит потери на их сопротивлении).
Все эти потери аккуратно собраны при расчёте электродвигателя тут:
https://disk.yandex.ru/i/g-KAG2M1kzfO_w
и тут:
https://disk.yandex.ru/d/KjWpjoV4GWtp9w
Разные потери и снижают КПД двигателя. Вечная задача – снижение потерь и рост КПД.
А вот так выглядят пластинки, по которым должны ездиь щётки, собирающие вырабатываемый ток:

Это - кровельное железо (другого у меня нет), прикрученное самыми маленькими шурупами, которые были в магазине. Щётка на пружине, конечно, по ним проедет. Но понятно, сколько энергии будет тратиться на езду по этим «ухабам» (за счет трения). Никаких подшипников у меня нет. Вместо них спица, вращающаяся в дырке. С потерями при трении щёток о железо не сравнить, но и это – потери на трении из-за общего несовершенства сборки и деталей.
Я думаю, что любой двигатель тех же размеров, собранный на заводе, действительно будет лучше этого в 10 раз. Просто потому, что технологии совершеннее и потерь будет меньше. Не сильно сомневаюсь, что что-то может настолько снизить потери по сравнению с тем, что было собрано на заводах относительно недавно.
А вот в снижение потерь процентов на 10 (и, соответственное увеличение выработки на это количество) поверю.
Например, пазы для намотки провода у меня круглые. Так исторически сложилось. Скорее всего, в металле их просто сверлят. Но печать на 3d-принтере позволяет сделать любую форму. В том числе можно сделать квадрат, в который влезет больше провода. Больше витков не надо. А если взять провод потолще, то снизятся потери на его сопротивление.
Потери на трение тоже могут снизиться при более качественном оборудовании, вытачивающем деталь. Идеальное даже на чертежах не бывает. Только в теории. Но если шарики в подшипниках станут более круглыми и менее квадратными, это снизит трение. Кроме того, катушка c проводами вращается между магнитами. Чем ближе магниты, тем лучше. Но чем меньше точность станка, тем больший зазор надо делать (на всякий случай). А если оборудование точное, то можно изначально предусмотреть меньший зазор и получить тот же прирост КПД. Так что, все возможно, но вряд ли в 10 раз.
|